Motivation and objectives
Since the performance of an aircraft is directly and inextricably linked to the performance of the propulsion system, efforts are constantly being deployed to increase both the thrust generation and the fuel efficiency of engines. The continuing demands for increased performance result in working very close to the aerodynamic, thermal and structural limits of the propulsion system. At the same time, the operating limits must be selected in such a way as to ensure safe operation even during transient emergency situations.
However, the deterioration of isolated or combined components leads to two negative effects:
- The distance to the operating safety limits are reduced
- Transient loads increase, driving the engine to the limits more quickly.
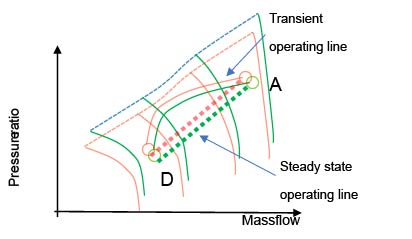
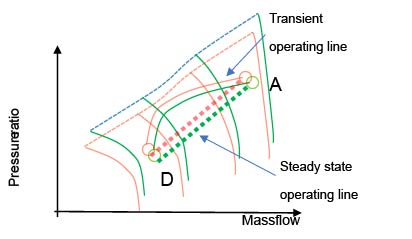
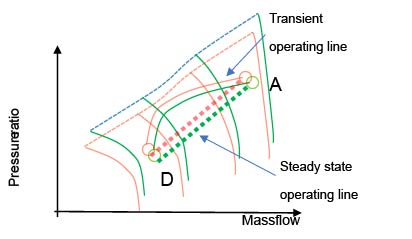
The objective of this subproject is to evaluate the influence of deterioration and repair on the steady-state and transient operating performance of engines. As an example, Figure 1 shows a repaired (green) and deteriorated (red) map of a compressor with a steady-state and transient operating line between the D and A operating points. The deterioration leads to a shift of the map to the lower left and of the operation line to the upper left. The transient operating line in particular thus comes very close to the stability limit.

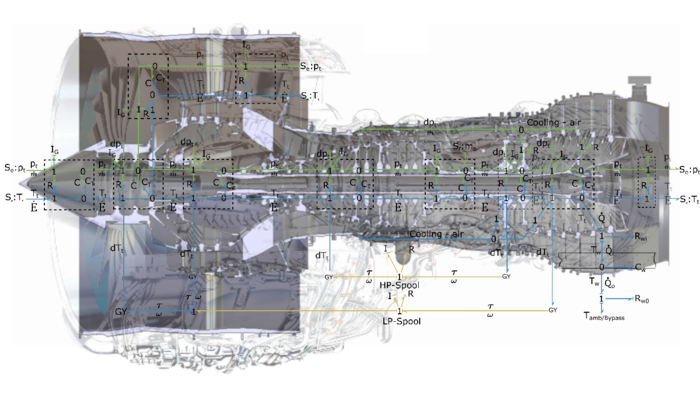
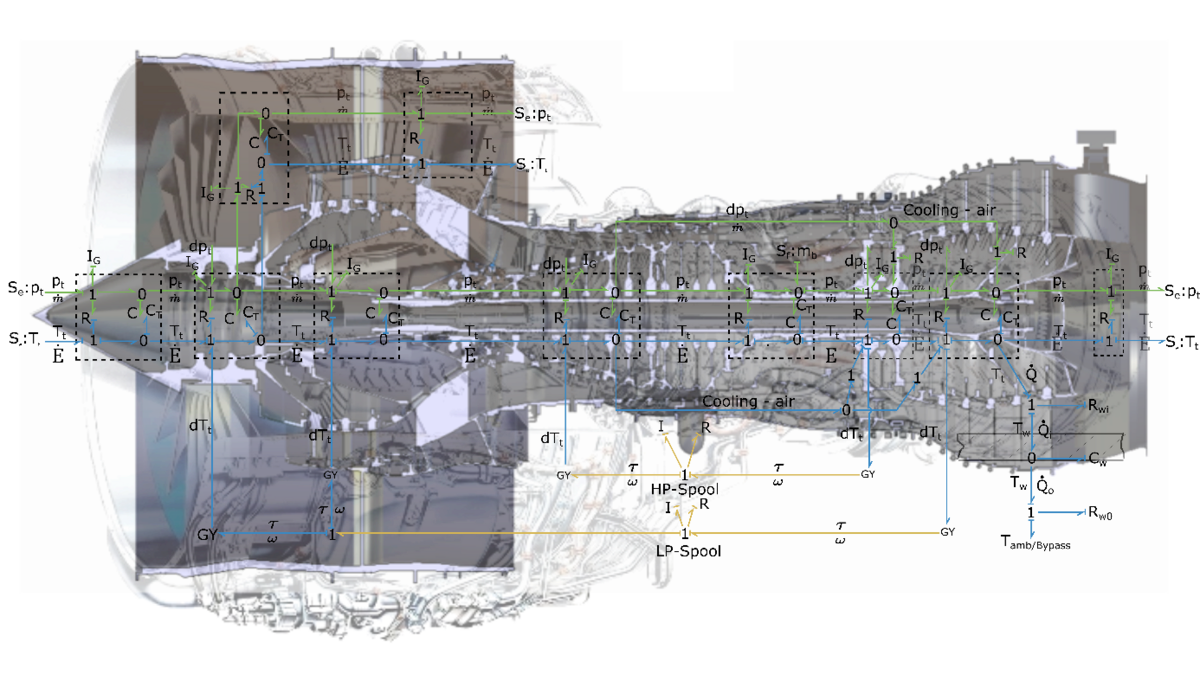
In order to investigate this influence as accurately as possible, the ASTOR (AircraftEngine Simulation for Transient Operation Research) performance calculation program is being developed in subproject D6, which discretizes the complete propulsion system using a finite difference method (FDM). For this purpose, the quasi 1D conservation equations for flow and energy transport, the dynamics of rotating machinery, friction and radial gap change due to heat transport in the engine are simulated. The resulting differential equation system is thus able to calculate the dynamic performance of the engine with interdependent interactions, allowing higher accuracies in the prediction of transient operation (compared to ordinary iterative performance synthesis methods). Figure 2 shows the IFAS research engine in the pseudo-bond graph notation representing the algorithm of ASTOR.
Results
In close cooperation with subprojects of the CRC 871 (e.g. A3, B3 and D5), a digital performance twin of the IFAS research engine of the V2500-A1 was created in ASTOR, which contains geometric information as well as the component-specific performance maps. This allowed the influence of deterioration on operational performance to be simulated and evaluated in several studies.

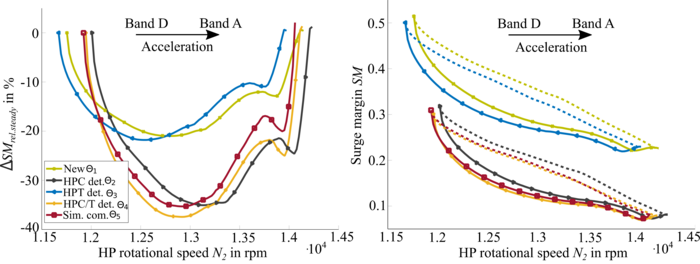
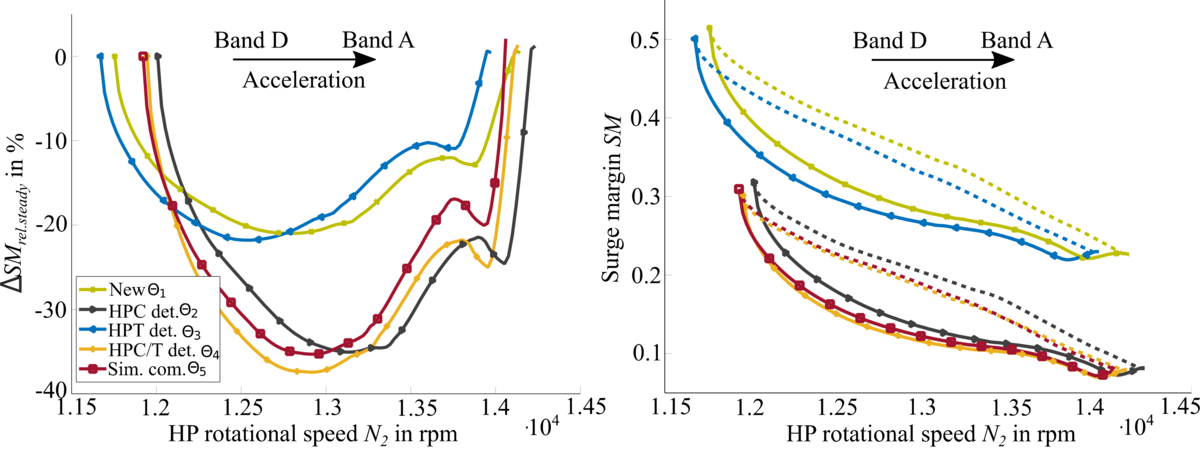
Figure 3 shows the transient operation lines of 5 different engines (Θ) at an acceleration between operation point D and A. The green line represents a new engine. The green line represents a new engine, blue represents an engine with a deteriorated high-pressure turbine, black represents a deteriorated high-pressure compressor, and red/yellow represents a deteriorated turbine and compressor. The right figure shows the distance to stability limit (SM) versus rotational speeds (with dots -transient, dashed -stationary). The left figure depicts the distance between transient and steady-state operating lines. Both figures show that the influence of a deteriorated compressor is much more critical for the stability limits than for the turbine, which was not evident when considering classical performance parameters.
Current research and outlook
In the upcoming stages of this project, extensive test runs with the IFAS research engine are planned, which are intended on the one hand to validate ASTOR experimentally, and on the other hand to investigate performance degradation caused by specific modifications. Together with subprojects A3 and A6, modifications will be made to the combustor whose influence will be measured at various positions of the engine in order to investigate the influence on the overall engine and to reflect this in ASTOR.

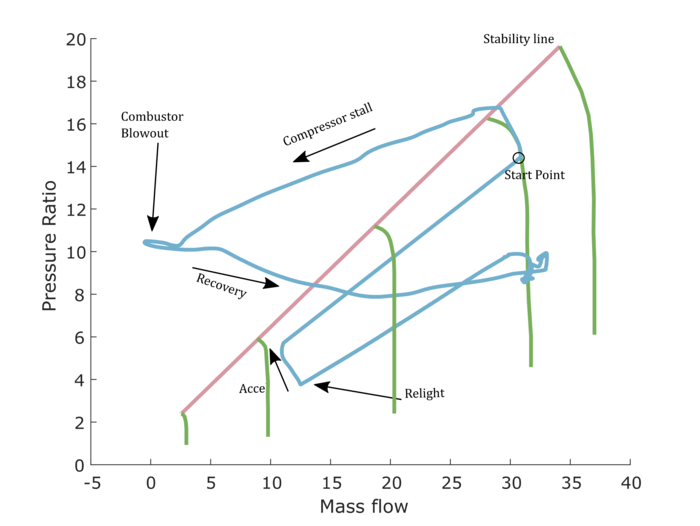
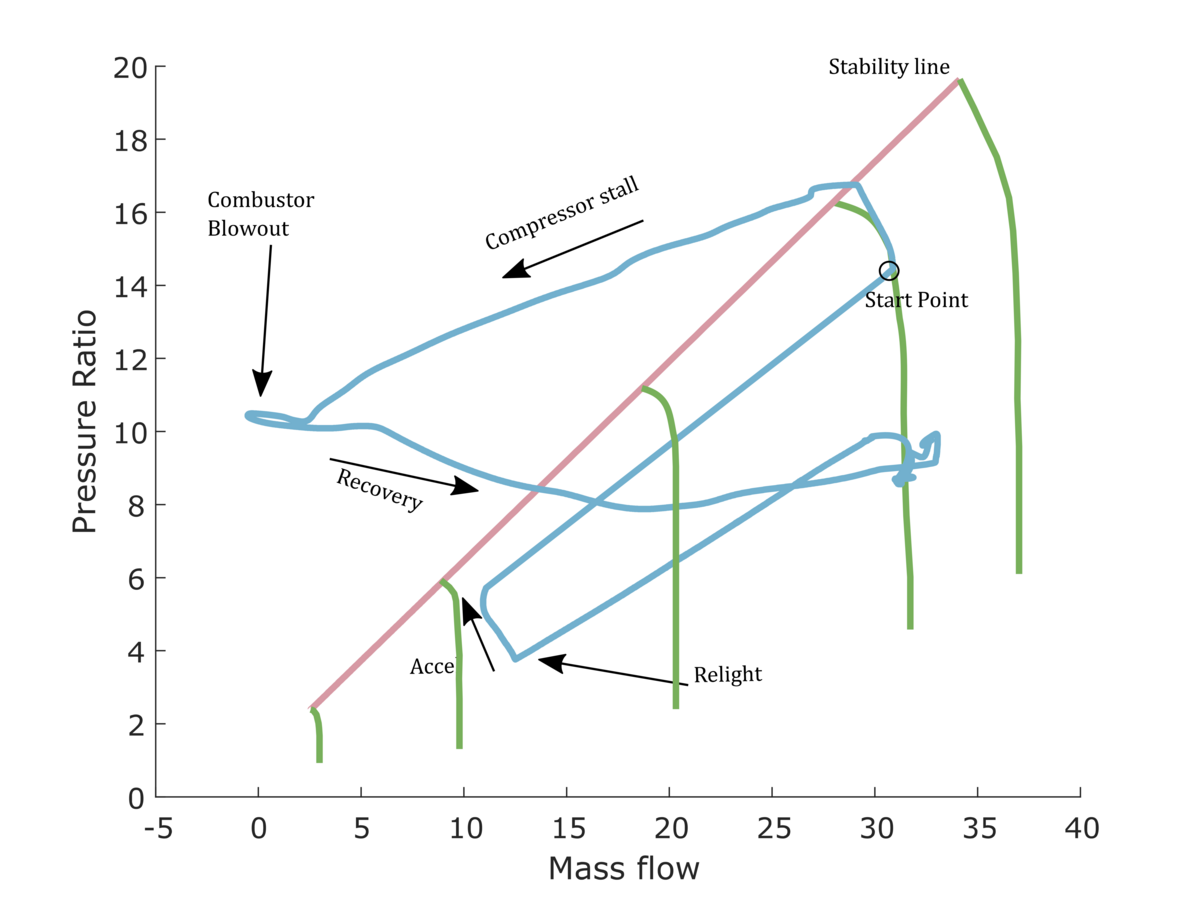
Furthermore, the FDM of the engine in ASTOR allows the simulation of highly dynamic effects, such as the deep rotating stall in the high-pressure compressor and the reaction of the overall system. As an example of this, Figure 4 shows the course of the high-pressure compressor during the deep stall. The characteristic curves shown in green represent the stable range of the high-pressure compressor and the engine up to the stability limit. If the compressor is throttled rapidly because the fuel is added too quickly (acceleration in an emergency), it can enter the unstable range, which would have fatal consequences for the turbofan engine.
Subproject leader
Hermann-Blenk-Strasse 37
38108 Braunschweig
Hermann-Blenk-Strasse 37
38108 Braunschweig
Staff
Hermann-Blenk-Strasse 37
38108 Braunschweig
Hermann-Blenk-Strasse 37
38108 Braunschweig
Publications
International Scientific Journal Paper, peer-reviewed
-
(2020): Influence of combined compressor and turbine deterioration on the overall performance of a jet engine using RANS simulation and Pseudo Bond Graph approach, J. Glob. Power Propuls. Soc. 4:296–308
DOI: 10.33737/jgpps/131109 -
(2019): Surface roughness of real operationally used compressor blade and blisk, Proceedings of the Institution of Mechanical Engineers, Part G: Journal of Aerospace Engineering, 1-10
DOI: 10.1177/0954410019843438 -
(2018): Deterioration effects of coupled blisk blades, J. Glob. Power Propuls. Soc. 2:465–476
DOI: 10.22261/JGPPS.CKB8N6 -
(2018): Surface Roughness Impact on Low-Pressure Turbine Performance Due to Operational Deterioration, J. Eng. Gas Turbines Power 140(6): 062601
DOI: 10.1115/1.4038246 -
(2018): Comparison of sensitivities to geometrical properties of front and aft high pressure compressor stages, CEAS Aeronautical Journal 9, 135–146
DOI: 10.1007/s13272-018-0281-8
International Conference Paper, peer-reviewed
-
(2020): System Dynamics of a Single-Shaft Turbojet Engine Using Pseudo Bond Graph, In: Dillmann A., Heller G., Krämer E., Wagner C., Tropea C., Jakirlić S. (eds) New Results in Numerical and Experimental Fluid Mechanics XII. DGLR 2018. Notes on Numerical Fluid Mechanics and Multidisciplinary Design, vol 142. Springer, Cham.
DOI: 10.1007/978-3-030-25253-3_41 -
(2020): Performance Simulation of Roughness Induced Module Variations of a Jet Propulsion by Using Pseudo Bond Graph Theory, Proceedings of ASME Turbo Expo 2020 Turbomachinery Technical Conference and Exposition GT2020
DOI: 10.1115/GT2020-14456 -
(2019): Jet Propulsion Engine Modelling Using Pseudo Bond Graph Approach, ASME Turbo Expo 2019
DOI: 10.1115/GT2019-90420 -
(2019): Simulation of the Impact of a Deteriorated High-Pressure Compressor on the Performance of a Turbofan Engine Using a Pseudo Bond Graph Modelling Approach, GPPS Peking 2019
-
(2019): Numerical Study of Stage Roughness Variations in a High Pressure Compressor, Gas Turbine Society of Japan (Hg.): Proceedings of the International Gas Turbine Congress 2019 Tokyo.