Motivation and objectives

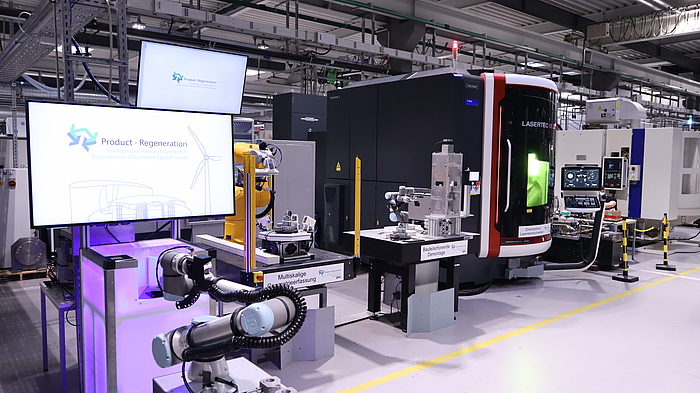
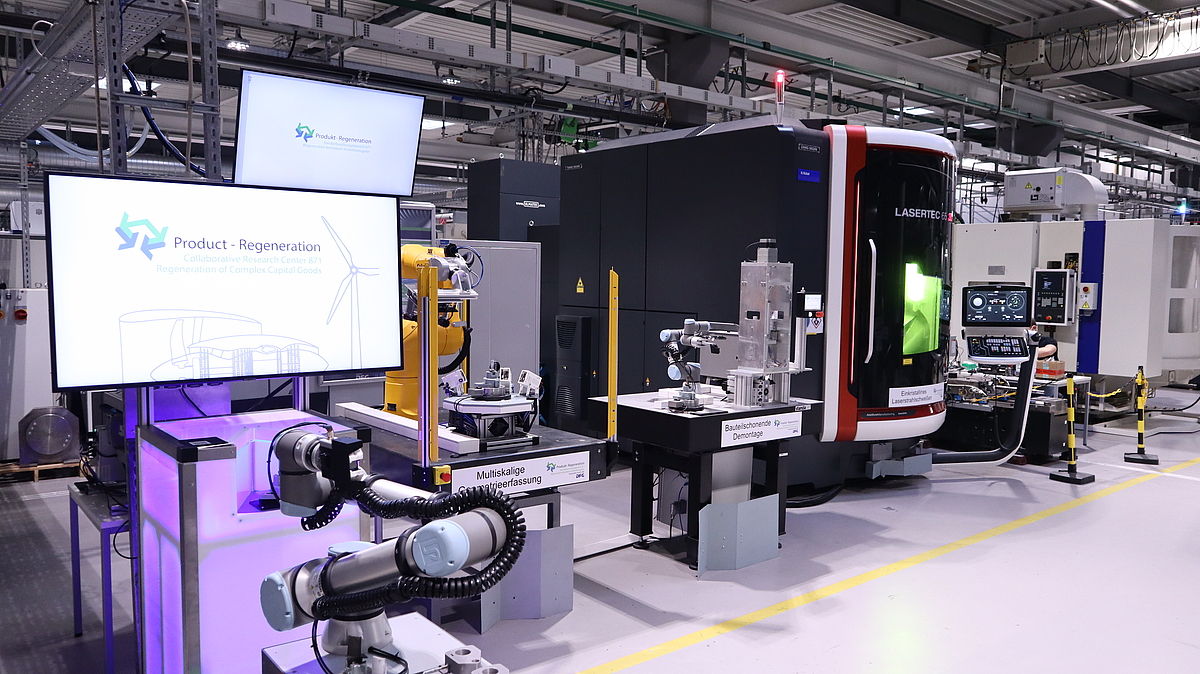
Within the Collaborative Research Centre (CRC) 871 a novel approach for the regeneration of complex capital goods was developed. A combination of virtual and real repair process was designed based on the example of the aircraft engine and in particular the turbine blade, in order to make rule-based decisions about the type and necessity of a repair based on a condition-based function quantification. The functional analysis in the virtual process enables an assessment of the service life of the component on the one hand and its influence on the performance on the other. On the basis of this information, the best possible path is then virtually evaluated, taking into account special customer requirements, and then executed using newly developed repair technologies. This innovative approach uses methods (e.g. numerical simulations of components and manufacturing processes) that are traditionally only used in product and manufacturing development and transfers them to the regeneration of complex capital goods for a model- or fact-based decision. In order to experience the benefits of linking virtual and real repair processes in their complexity as examples, guests from industry and research will be able to personally experience this from November 2020.
Please note that activating the video will result in the transfer of data to the respective provider. Further information can be found in our privacy policy.
Play video
Animated preview of the system demonstrator
Results
In order to consider the feasibility of an automated repair process for turbine blades not only theoretically, a system demonstrator will be set up in this subproject. In this demonstrator, all technologies for regeneration will be combined as a "proof-of-concept" and then presented to interested parties from industry and research. The regeneration process begins with the dismantling, followed by the condition assessment, the technical simulation and the economic evaluation up to the execution of the repair and the subsequent quality assurance. In addition to demonstrating the research content of the repair process, the focus is on investigating the interactions of the individual repair steps by implementing a consistent data and material flow. The aim is to further coordinate and develop the individual processes and networking. The findings and processes are not only limited to turbine blades, but can also be transferred to other complex capital goods such as stationary gas turbines or wind turbines.
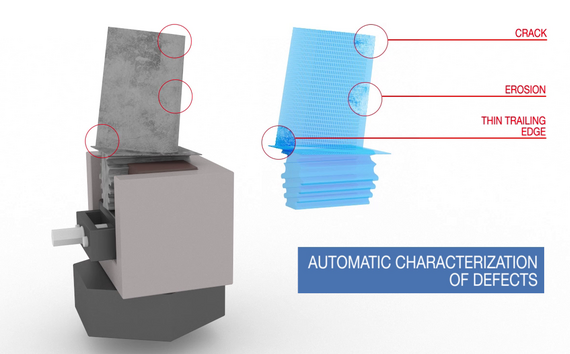
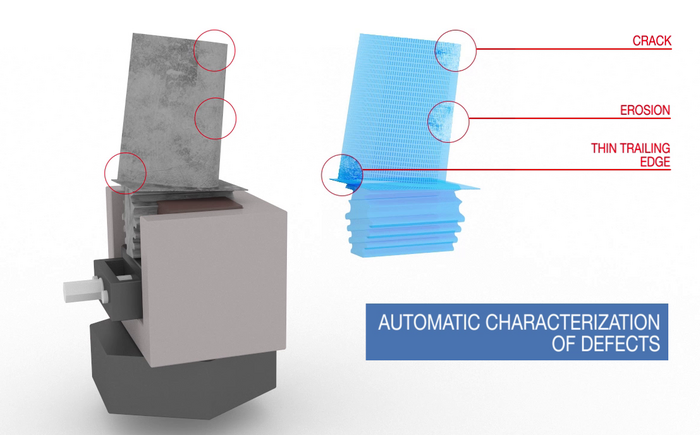
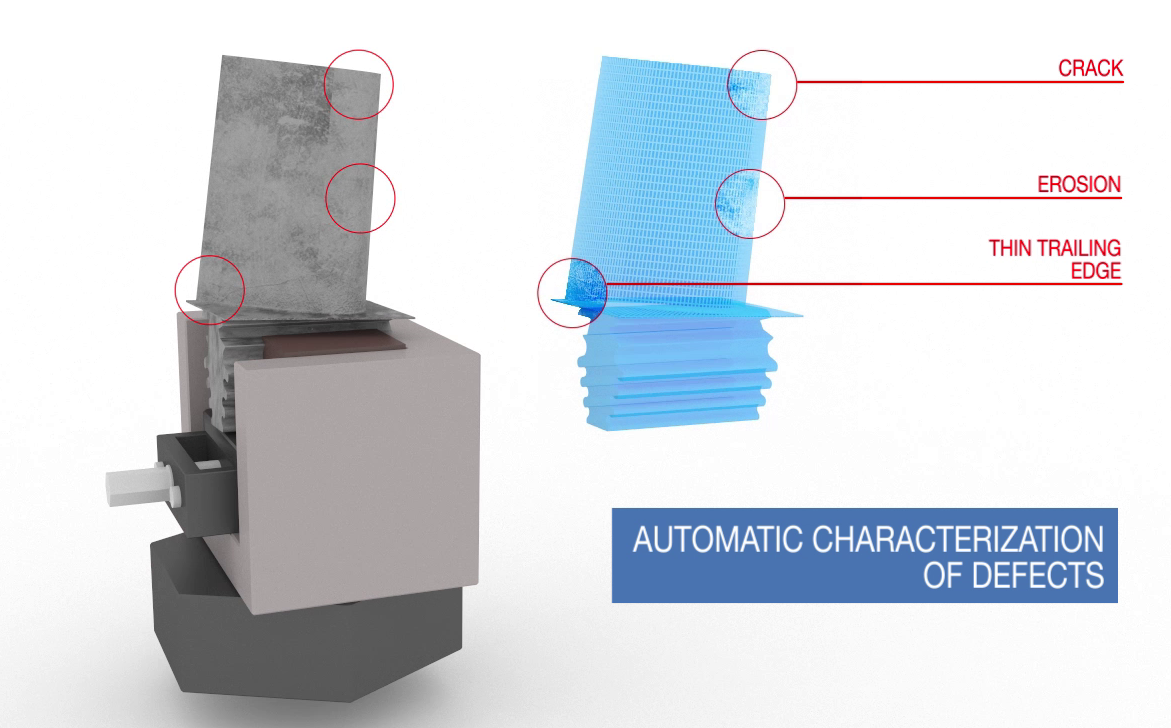
Current research and outlook
The system demonstrator is currently being set up at the LUH's Technical Production Centre. Current work steps are the elaboration and implementation of the consistent data flow as well as the detailed planning of the plant concept. From 2019, the construction of the individual process cells, including the commissioning of subsystems, will begin. The entire plant will be operational at the beginning of 2020 so that the continuous regeneration process can be set up. To experience the system in person, be our guest at the demonstrations from November 2020. In the meantime, Mr. Nicolas Nübel will be happy to answer any further questions you may have.
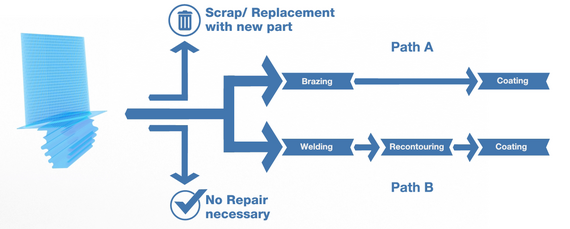
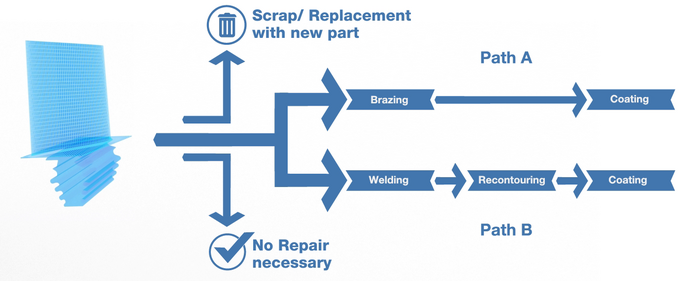
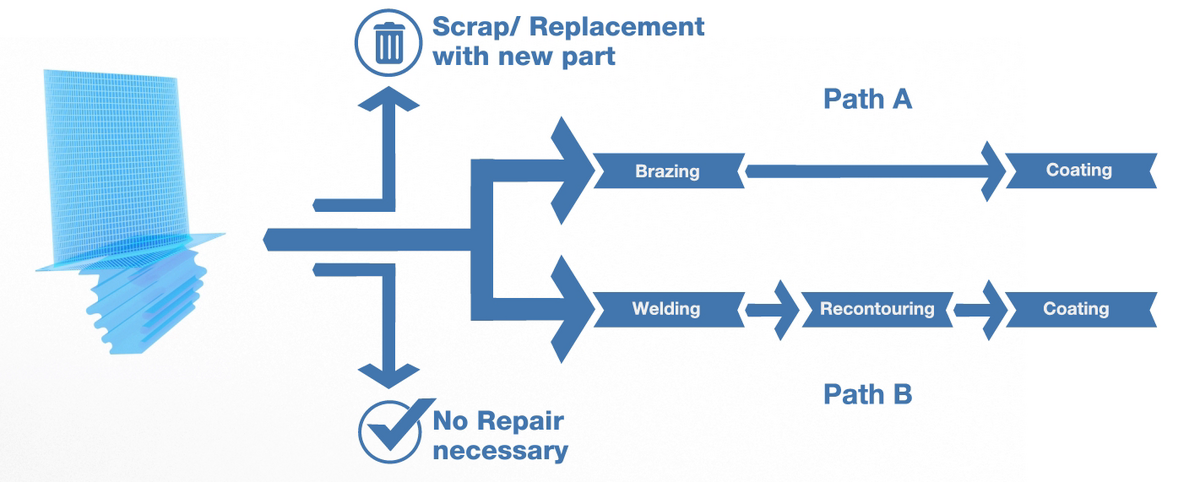
Subproject leader
30823 Garbsen
30823 Garbsen
30823 Garbsen
Staff
Publications
International Scientific Journal Paper, peer-reviewed
-
(2022): A regeneration process chain with an integrated decision support system for individual regeneration processes based on a virtual twin, International Journal of Production Research
DOI: 10.1080/00207543.2022.2051089 -
(2019): Towards an autonomous maintenance, repair and overhaul process, Procedia Manufacturing 40, S. 77–82
DOI: 10.1016/j.promfg.2020.02.014
International Scientific Journal Paper, not peer-reviewed
National Scientific Journal Paper, not peer-reviewed
-
(2020): Einsatz eines virtuellen Werkstückzwillings - Für die digitalisierte und vernetzte Instandsetzung von Hochdruckturbinenschaufeln, WB Werkstatt und Betrieb, Bd. 153, S. 43
-
(2019): Automatisierte Regeneration von Triebwerkskomponenten - Zustandsbasierte Regeneration von komplexen Investitionsgütern, MAV, S. 100–102 More info
National Conference Paper, not peer-reviewed
-
(2020): SFB 871 – Regeneration komplexer Investitionsgüter Systemdemonstrator, New Production Technologies in the Aerospace Industry, Bd. 2020, S. 39–52