Motivation und Zielsetzung
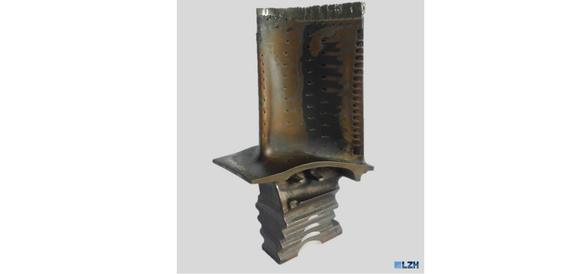
Turbinenschaufeln aus Flugzeugtriebwerken werden abhängig von ihrer Funktion und insbesondere Position aus unterschiedlichen Werkstoffen hergestellt. Um die steigenden Ansprüche an diese Triebwerke realisieren und gleichzeitig die Effizienz der Triebwerke steigern zu können, werden einkristalline Nickelbasis-Superlegierungen für Hochdruckturbinenschaufeln eingesetzt. Sie erfahren hohe thermische sowie mechanische Belastungen, die zu Verschleißerscheinungen, wie beispielsweise in Form von Rissbildungen im einkristallinen Grundmaterial, führen. Im Rahmen des Teilprojektes B5 wurde die grundlegende Instandsetzung defekter, einkristallin hergestellter Hochdruckturbinenschaufeln untersucht. Im darauf aufbauenden Transferprojekt T5 werden die gewonnen Erkenntnisse unter industriellen Bedingungen auf Turbinenschaufeln übertragen, die sowohl in ihrer Materialzusammensetzung als auch Geometrie abweichen. Dieser Transfer ist essentiell für eine Reparatur verschiedener Turbinenschaufeln, da der Reparaturerfolg eine Materialabhängigkeit vorweist.
Das Vorhaben gliedert sich in drei wesentliche Bereiche. Im ersten Bereich wird die Instandsetzung von defekten, einkristallinen Laufschaufelspitzen betrachtet. Der zweite Bereich beinhaltet die Reparatur von Leitschaufeln. Diese weisen im Vergleich zu der Laufschaufel nicht nur eine stark abweichende Geometrie und Materialzusammensetzung auf, sondern auch verschiedene Schadensbilder. Die Entwicklung und Umsetzung von schadensbildabhängigen Reparaturverfahren steht hierbei im Fokus. In dem dritten Bereich wird das Ziel verfolgt die untersuchten Schäden mitsamt den hierfür entwickelten Reparaturstrategien in einer Datenbank festzuhalten. Die Motivation ist das anwenderfreundliche Anbieten von schadensbildabhängigen Reparaturvorschlägen.
Ergebnisse
Auf Basis des Teilprojektes B5 konnte das Reparaturverfahren grundsätzlich auf dieses Projekt transferiert werden. Notwendige Materialien und Mittel wurden zur Regeneration bereitgestellt. Die Reparatur erfolgt im Rahmen der additiven Fertigung in Form des Laserauftragschweißens. Aufgrund der zum Teilprojekt B5 abweichenden Materialzusammensetzung der Hochdruckturbinenlaufschaufel wird der Prozess an die neuen Bedingungen angepasst. Des Weiteren konnten in enger Absprache mit dem Projektpartner die verschiedenen Fehlerbilder der Leitschaufel kategorisiert werden.
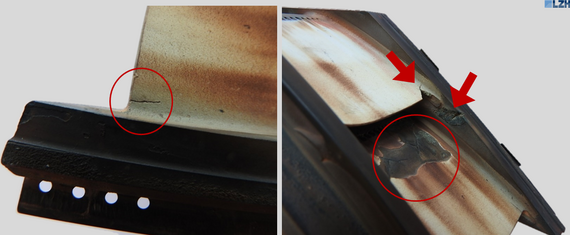
Aktuelle Arbeiten und Ausblick
Im weiteren Verlauf wird die Reparatur den Anforderungen entsprechend optimiert. Hierzu zählt die Steigerung der Prozessgeschwindigkeit, um die Grenzen dieses Verfahrens effizient ausschöpfen zu können. Darüber hinaus wird die Reparatur an Hochdruckturbinenleitschaufeln erfolgen. In diesem Rahmen wird der Reparaturprozess materialspezifisch optimiert. Durch die Einarbeitung der Ergebnisse in die Schadensdatenbank wird die Möglichkeit zur Reparatur auf weitere Schadensbilder erweitert. Grundsätzlich erfolgt ein Austausch der resultierenden Erkenntnisse aus dem Transferprojekt T5 mit den themenbezogenen Teilprojekten des SFB- 871. Somit soll die Anwendbarkeit der Rekonturierungsprozesse praxisnah erfolgen.
Verantwortliches Institut
Das Projekt wird verantwortet durch das Laserzentrum Hannover e.V.
Teilprojektleiter
Hollerithallee 8
30419 Hannover
Hollerithallee 8
30419 Hannover
Hollerithallee 8
30419 Hannover
Hollerithallee 8
30419 Hannover
Mitarbeiter
Hollerithallee 8
30419 Hannover
Hollerithallee 8
30419 Hannover